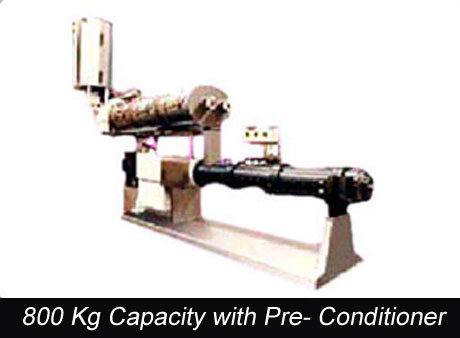
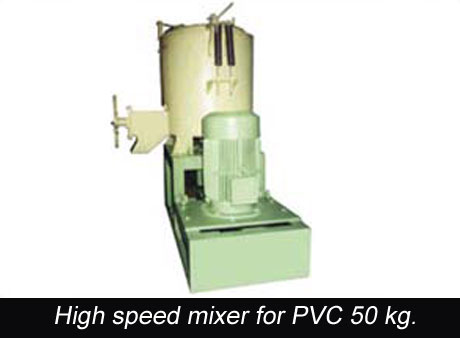
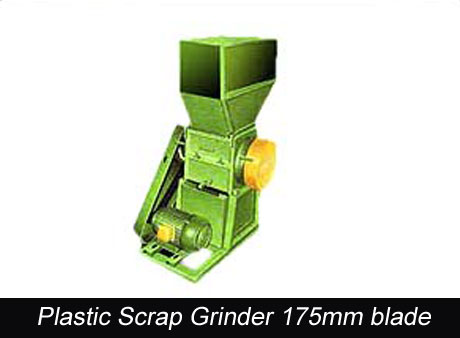

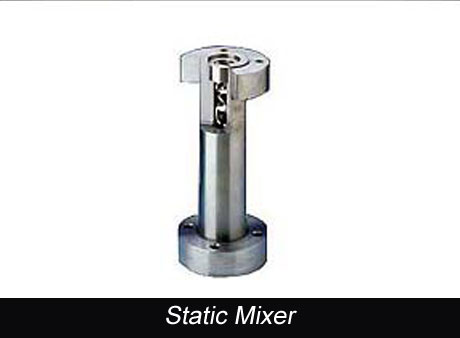



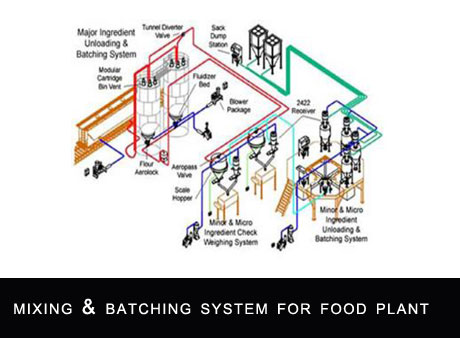
1. WELL GRIND Plastic Scrap Grinders from 1 HP to 10 HP.
2. MIX-O-WELL High speed PVC Compounding & Preheating mixers 50 Kgs/batch capacity.
3. Extruder Instrumentation & control panels for temperature, motor speed control, pressure measurement and controls,
process automation.
4. Crammer Feeder for feeding light-weight, difficult-to-feed materials in Extruder.
5. Extrusion Dies & Tooling.
6. Static Mixers as the name suggests have stationary (static) mixing elements which induce circuitous flow of polymeric
materials and ingredients, at near low shear by splitting and re-uniting streams of material and ingredients .
They are generally used where the ingredients can’t withstand high shear using normal mixers.
7. Hydraulic Screen Changers for Plastic Extruders.
8. Pneumatic Conveying System for transporting particles ranging from fine powders to pellets and bulk densities of 16 to
3250 Kg/m^3
A pneumatic conveying system is a process by which bulk materials of almost any type are transferred or injected using
air as the conveying medium from one or more sources to one or more destinations. A well designed pneumatic conveying
system is often a more practical and economical method of transporting materials from one point to another than
alternative mechanical systems (belt conveyors, screw conveyors, vibrating conveyors, drag conveyors and other methodologies)
The Dilute phase Pneumatic Conveying System (PCS) is commonly used in many industry like Plastic, Chemical, Food processing,
etc. wherever solid particles need to be moved from one point to another, or from one point to multiple points or vice-versa.
The particles are held in suspension as they are moved through lines by high volume, high velocity, pressurized air.
The arrangement is very simple without much complications.
For more details, please refer to the Brochure on PCS by following Download-Brochure Link.
We also manufacture Single/Twin screw and barrels for Extruders (Plastic, Food or Rubber) and Injection Moulding
machines, up to 150mm dia. in any L/D ratio. Whether your requirement is for existing or you need new design,
leave the problem to our team of experts!
Screws are usually made from 4140 grade steel, stress relieved and hardened to 32 Rc with the screw OD flame hardened,
hard faced with Stellite 6 or tungsten carbide coating. Other materials like Nitralloy or Stainless steel are also selected.
The common materials for the barrel are D2 steel hardened or Nitralloy steel gas nitrided. Hastalloy can be offered
for processing polymers with abrasive fillers, e.g. glass fibres.
The single screws for plastics are usually of solid construction while twin screw can be solid or in segments.
The separate segments fit on central splined shafts and the geometry can be easily adjusted to suit processing task.
Food Extruders usually employ segmented screws for most applications and the barrels are having spiral or straight
grooves for more material movement and output.
For special projects, we have built machines using feed screws/barrels which are designed to work continuously at temperatures in excess of 500 C. These screws and barrels not only use special materials (screws use hard faced flights with special weld materials) and the barrel made from Hot Die Steel which is heat treated to retain hardness at elevated temperatures. Example of such project is the extraction of carbon black powder from pulverized rubber scrap in suitable Reactor designed for purpose. Two 50mm single screws were used for drawing out the carbon black powder by feeding scrap rubber by 2 nos. 90mm single screws at elevated temperatures in excess of 500 C.
These Screws were made for High Temperature used in above Reactor.